A solid-liquid mixing reactor based on swirling flow technology
- Rafal Tekreeti
- Oct 9, 2023
- 3 min read
By: Zhu Yang, Thomas Holemans and Maarten Vanierschot

Solid-liquid mixing is a critical process in the chemical industry and is widely used for various operations. Mechanical stirred tanks have historically dominated this field due to their improved energy efficiency over the years. However, they have major sealing problems with the inherent drive shafts of the stirred tanks, especially when dealing with extreme operating conditions (high temperatures and pressures) when scaling up to industrial production volumes. To address these challenges and promote the commercialization of industrial technologies that are subject to this constraint, such as Reductive Catalytic Fractionation (RCF), the ‘Applied Fluid Mechanics and (Aero)Acoustics’ (AFAA) research group of the Department of Mechanical Engineering, KU Leuven has developed a novel solid-liquid mixing technology called the Swirling Flow Reactor (SFR).
The VSC Computation Center played a pivotal role in this research by providing the computational resources necessary for the CFD modelling of the Swirling Flow Reactor.
Swirling flows, known for their effectiveness in improving mixing, play a crucial role in the SFR's design and functionality. The flow and mixing in the SFR are driven by the swirling jet, which does not require a mechanical shaft for energy transfer and, therefore, eliminates any sealing problems. In practice, the Swirling Flow Reactor (SFR) is integrated into a fluid loop system. Within the SFR, solid particles are contained within the mixing vessel itself, thanks to the strategic placement of a filter at the top. The high homogeneity achieved with this system is depicted in Figure 1.
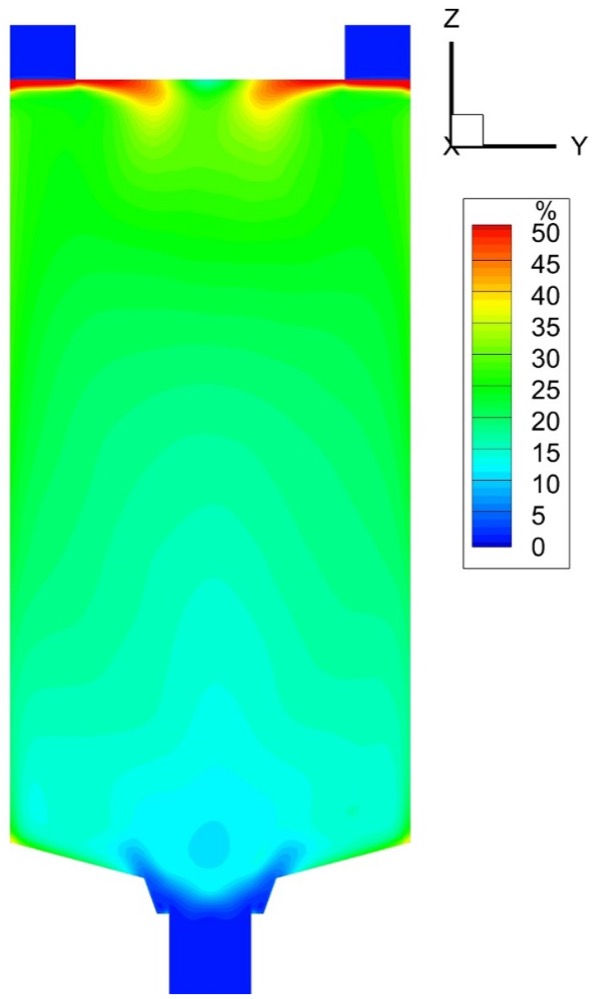
Figure 1:Time-averaged distribution of solid concentration in the mixing vessel. The swirling fluid flow inlet is situated at the bottom, and the particles are constrained in the mixing vessel itself by a filter at the top (outlet).
The study investigates the mixing mechanism and performance of the SFR using Computational Fluid Dynamics (CFD) modelling via the VSC HPC, offering valuable insights into flow structures and particle distribution within the reactor. The swirling flow reactor demonstrates a satisfactory mixing, which is shown in Figure 1. In addition, the swirl jet formed a Coanda jet flow (CoJF) with the specially designed inlet nozzle, which plays an important role in washing the reactor bottom surface. More specifically, this CoJF is the bulk flow attaching to the bottom wall of the SFR, as depicted in Figure 2. Additionally, Spectral Proper Orthogonal Decomposition (SPOD) is used to identify and reconstruct the Precessing Vortex Cores (PVCs) in the CoJF, as shown in Figure 2. PVCs have strong fluctuations and promote mixing.
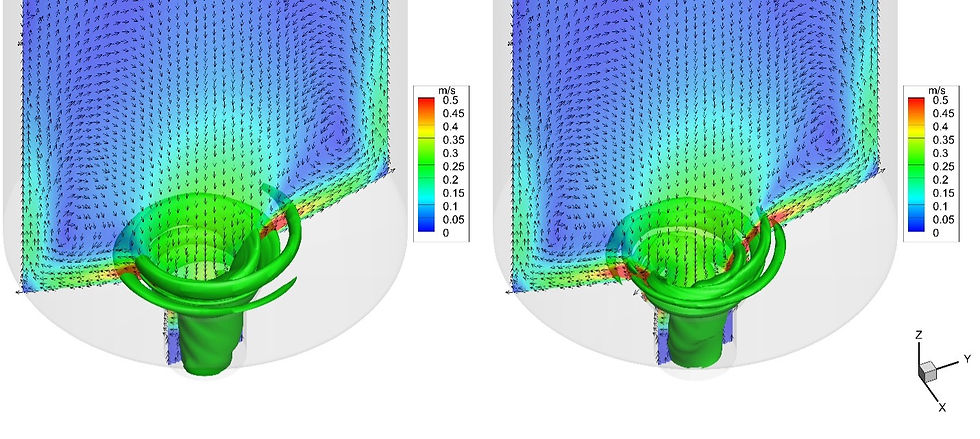
Figure 2: Instabilities and flow field in SFR, more specifically in the nozzle. The left figure shows a local minima, while the right figure shows a local maxima, alternating each other periodically. The rotating structure visible is a Precessing Vortex Core, which promotes mixing downstream.
The Flemish Supercomputer Center (VSC) played a pivotal role in this research by providing the computational resources necessary for the CFD modelling of the Swirling Flow Reactor. The complex multi-scale/frequency flow structures of the SFR and the need to simulate particle-dense multi-phase mixing presented significant computational challenges. The VSC's HPC infrastructure, specifically the efficient multi-core CPU parallel computing capabilities, enabled the researchers to conduct detailed simulations, gaining a comprehensive understanding of the reactor's flow structure and mixing performance. This computational support was instrumental in advancing the development of the Swirling Flow Reactor and its potential applications in industrial-scale solid-liquid mixing.
Read the full publication of this article at ScienceDirect